Food Carton Sealing: Tests and Developments
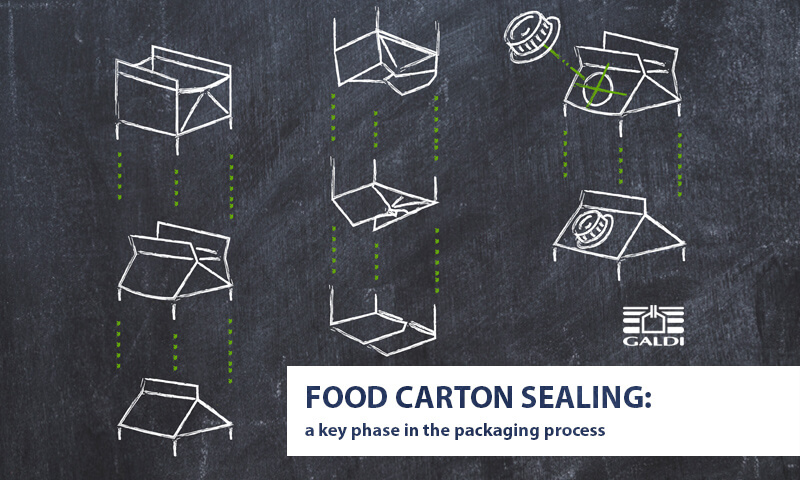
The folding and sealing of food cartons play a key role in packaging processes.
They are essential to ensure both constant production levels and optimal sealing performance, and therefore also:
- Shelf life accuracy
- Contamination risk reduction
Over the years, Galdi's research team has made continuous improvements in order to have a hyper-precise, "robust" and reliable folding and sealing system.
The cooperation with leading food carton manufacturers has been invaluable to carry out sealing and filling tests to validate new carton types.
Recently we have also collaborated with the Mechanical Engineering Department of the University of Padua. The goal of the study was to gain scientific insight into how different cardboard types react to packaging processes.
The results, which confirmed some configurations that up to then had only been assessed through practice, enabled us to further optimise the process.
THE STAGES OF THE SEALING PROCESS
Top folding and sealing
The first challenge for Galdi designers is to offer a top folding and sealing system that guarantees utmost precision and efficiency.
This is the most critical and important phase to avoid problems linked to sealing resistance and contaminations.
A proper set-up – both in terms of temperature and mechanical settings (e.g. top press adjustments) – is also essential to ensure that food cartons are perfectly sealed. This is, in fact, the first item to be checked when troubleshooting malfunctions.
The post-installation training for operators and maintenance technicians is therefore important to guarantee that the system is fully efficient. Operators can so carry out the necessary adjustments and maintenance technicians will be able to quickly find the cause of a problem, even when this is not in the station itself (due, for example, to imprecise chain movement or incorrect dosage).
Bottom forming
From an aesthetic point of view, well aligned bottoms with perfectly folded corners provide the clearest indication of a well-designed filling machine.
Keeping in mind that a problem in the bottom forming system is one of the main causes of downtimes, it's not surprising that its efficiency over time is also a decisive factor.
Given the high filling speed of Galdi's RG270 filling machine, many tests and trials were conducted on its bottom forming station in order to reach the best possible results, regardless of packaging solution.
Designers and testers validated and tested many cardboard typologies. Each paper type reacts differently to the packaging and sealing process.
An optimal set-up of the bottom forming station is also necessary to make sure that excessively high temperatures do not affect the aftertaste of a product.
A case in point is the project for the first filling machine for water in gable top cartons in Italy. Our designers conducted in-depth research and optimisation work to come up with ideal configurations and temperatures, so as to avoid taste alteration.
Cap welding
Though being less complex and "delicate" than the bottom forming and top sealing systems, a cap feeding system for gable top packaging must ensure uniform weld quality. The heat produced during the process shall not interfere with the top forming phase, nor damage the cap itself, causing filaments.
With this goal in mind, we performed numerous packaging tests on a variety of caps in different shapes, sizes, plastic and flange types. Needless to say, research is ongoing, as new cap typologies, like bio-based caps, have entered the market.
Besides performance tests, we have also carried out research on energy consumption during the sealing of food cartons. In light of the results, we developed
a new heating system, which is more complex, better performing and more precise, but less energy-intensive.
Research in this area continues as well.
Stay tuned for future developments!