RG280: Galdi's Gable Top filler with consistent hygienic performance
Superior and, above all, consistent hygienic performance: this is what makes the RG280 a one-of-a-kind Gable Top filler!
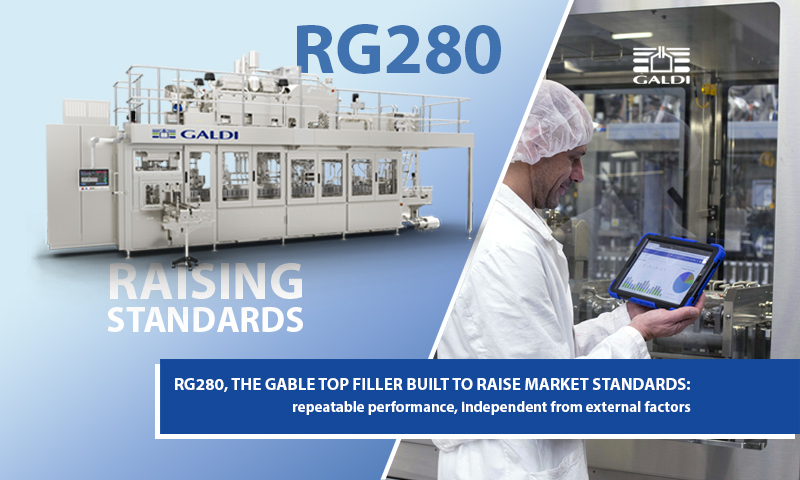
Thanks to the solutions we developed for the RG280, we were able to bring to market a Gable Top filling machine featuring superior hygienic performance.
No doubt this is an important achievement, but what really matters is making sure that these performance levels remain consistent over time!
Looking at the whole packaging process, Galdi engineers and specialists analysed, developed and implemented a number of technical solutions to ensure that performance is repeatable and independent from external factors.
PACKAGE AND CAP DISINFECTION
With the help of simulations, we developed a clever design for the area, for the disinfection tunnel in particular, optimising the process further.
Besides ensuring a logarithmic count reduction in line with VDMA requirements for aseptic fillers, the use of vaporized hydrogen peroxide (35% solution) removes the limitations of systems that use 3% peroxide solutions. Therefore, poor disinfection due to improper concentration and the problems resulting from the decay of hydrogen peroxide over time are no longer a risk.
The RG280 guarantees superior hygienic standards throughout the process, while removing the risks due to changes in environmental conditions and use.
SIP STERILIZATION
Thanks to the fully automated SIP process, which uses pressurised steam, the RG280 guarantees consistent performance levels, regardless of:
- Human error
- Improper chemical use
- Changes in temperature, concentration and time parameters, as is typically the case with systems using chemicals at different temperatures
Compared to cold sterilization with peracetic acid, the efficacy of steam sanitisation can also be guaranteed over time, since the risk of microorganisms developing resistance to disinfectants is removed, and with it the occurrence of inconsistent performance in the middle and long term.
Finally, a thorough sterilisation ensures that superior hygienic levels are achieved in the most difficult parts of the filler too.
HYGIENIC CHAMBER
Thanks to testing and simulations, we improved the way air flows are handled within the filler's hygienic chamber. Air entering the chamber is cooled, micro-filtered (through a MOCA/FCM certified HEPA filter) and dehumidified to reduce the risks of recontamination and ensure the best possible air quality.
We developed a truly self-adaptive system capable of continuously adjusting to changing conditions.
The results? A more controlled process, a considerable reduction in recontamination risk and consistent performance.
EXTERNAL CLEANING
For the development of the RG280, classic foam cleaning was discarded in favour of an external cleaning system with recirculating soda and acid, which is safer and more effective.
The external cleaning and disinfection system was tried and tested to ensure a uniform, accurate, repeatable and thorough cleaning of the machine.
To minimize the contamination risk due to human error, we opted for automatic cleaning for the air ducts too, so that the process is now fully automated.
CARTON SEALING
In line with the “Raising Standards” concept that drove the development of the RG280, our pack acceptance specifications are now even stricter, both in terms of tightness and aesthetics.
The new criteria were tested repeatedly on all available formats in order to give you the same guarantees, regardless of fill volume (from 250ml up to 1ltr packs with cap closure).
Combined with thorough studies on performance repeatability, the new standards contribute to:
- Reducing product and packaging waste
- Reducing contamination risks
- Maintaining the product's organoleptic qualities for the entire shelf life
- Achieving better and lasting aesthetic quality
To sum up, the RG280 stands not only for the highest levels of hygienic performance, but also embodies the concept of "Robustness", which is very dear to our company.
Reflecting this very principle, here are the unique characteristics of Galdi's packaging systems:
- Compatibility with all commercially available paper types
- Adaptability to production environment conditions
- Integration with already existing systems (e.g., ERP)
- Performance repeatability over time
- Multi-format configurations
- Easy upgrade thanks to modular design
Want to find out all about the new RG280?